|
|
|
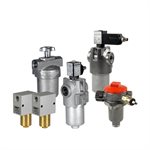 Filter
|
|
|
|
|
Providing contaminated lubricants for friction points can shorten operating life, cause premature failure, and accelerate the aging of lubricants. Lubricants are likely to be contaminated during or after production. Non lubricant, insoluble solid particles in oil, and the aging of the lubricant itself will be a source of contamination. Full filtration can significantly prolong the service life of equipment, bearings and other friction points. Key selection criteria: Nominal flow [l/min], pressure drop (depending on capacity and viscosity) Operating pressure [MPa] Filter pore size, filtration ratio, ACFTD capacity temperature range Auxiliary equipment, such as visual dust indicator, electronic dust indicator, bypass valve Bearing seat, seal, filter material Filter for centralized lubrication system: Standard filter (DIN 24550) Suction filter / strainer Pressure filter (in mainstream and bypass flow) Reflux filter Aeration filter for liquid storage tank Filter screen Disc filter When positioning the filters in the fuel tank or the system, make sure they are accessible and easy to replace. The piping used in the centralized lubrication system shall be cleaned (flush) before assembly. Technical features: Compatible with the following oil: the highest NLGI level 00 of lubricating oil and grease Ambient temperature: -30 to +100 DEG C Pressure: up to 100 bar Volume flow: 40 - 100 L Characteristic: Glass wool - inorganic fiber - absolute filtration Wire mesh stainless steel standard filter |
|
 |
|
|
|
|
|